Hydraulic pumps are integral to various industrial, construction, and automotive systems, transforming mechanical energy into hydraulic energy. These pumps create the flow of hydraulic fluid, enabling systems to perform work like lifting, pressing, or moving heavy loads. In this article, we’ll explore the functionality of hydraulic pumps, the different types available, and their common applications.
1. What is a Hydraulic Pump?
A hydraulic pump is a mechanical device that moves hydraulic fluid through a system, converting mechanical power into hydraulic energy. The pump creates a flow of fluid that is then used to perform work in hydraulic machinery. By pressurizing the fluid, the pump allows for the transfer of energy, which powers various actuators like cylinders and motors.
2. How Does a Hydraulic Pump Work?
Hydraulic pumps operate based on the principle of displacement. As the pump rotates or moves, it creates a vacuum that draws hydraulic fluid into the pump. The fluid is then pressurized and forced through an outlet into the hydraulic system.
The amount of flow generated by the pump depends on its size and speed. The pressure within the system is determined by the resistance to flow, typically created by the machinery or components that the pump is driving.
3. Types of Hydraulic Pumps
There are several types of hydraulic pumps, each suited to different applications. The most common types include:
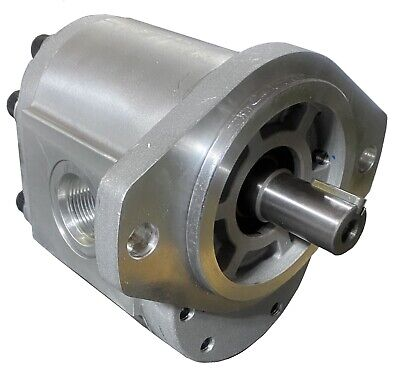
a) Gear Pumps
Gear pumps are one of the most commonly used hydraulic pumps. They operate by using the meshing of gears to pump fluid by displacement. There are two main types of gear pumps:
- External Gear Pumps: Use two gears that rotate in opposite directions to create flow.
- Internal Gear Pumps: Have one external gear and one internal gear, used to move fluid in a continuous motion.
Advantages:
- Simple design and easy to maintain.
- Reliable and durable.
- Cost-effective.
Applications:
- Construction equipment.
- Agricultural machinery.
- Hydraulic presses.
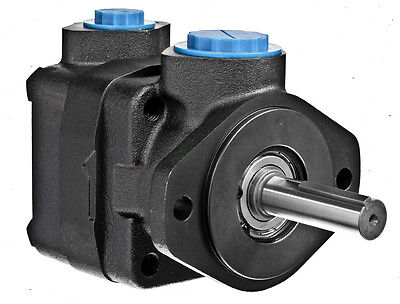
b) Vane Pumps
Vane pumps use a series of vanes, mounted to a rotor, to create a vacuum that draws hydraulic fluid in. As the rotor spins, the vanes extend and retract, creating pockets of fluid that are pressurized and expelled from the pump.
Advantages:
- Smooth operation with minimal pulsation.
- Higher efficiency compared to gear pumps.
- Quiet operation.
Applications:
- Power steering systems in vehicles.
- Injection molding machines.
- Hydraulic lifts and cranes.
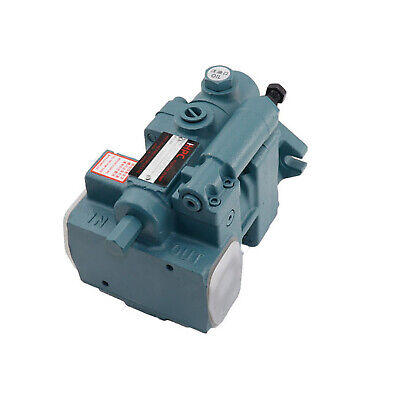
c) Piston Pumps
Piston pumps are more complex than gear and vane pumps but are also more efficient and capable of generating higher pressures. These pumps use pistons that move back and forth within a cylinder to create pressure. There are two main types of piston pumps:
- Axial Piston Pumps: Have a row of pistons that move in parallel with the pump’s axis.
- Radial Piston Pumps: The pistons move perpendicular to the axis of the pump.
Advantages:
- High-pressure capabilities.
- Greater efficiency and precision.
- Suitable for demanding industrial applications.
Applications:
- Heavy-duty construction equipment.
- Aerospace systems.
- Hydraulic presses and forging machines.
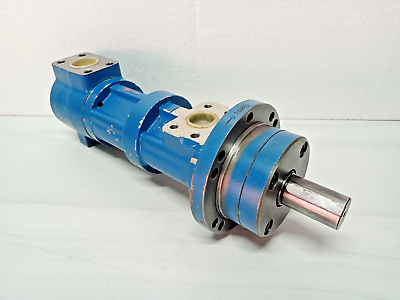
d) Screw Pumps
Screw pumps use two or more interlocking screws to move fluid through the pump. These pumps are designed to handle high-viscosity fluids and operate quietly.
Advantages:
- Ideal for high-pressure, low-flow applications.
- Capable of handling a wide range of fluid viscosities.
- Low noise levels.
Applications:
- Oil and gas industry.
- Shipbuilding.
- Industrial hydraulic systems.
4. Key Components of Hydraulic Pumps
Hydraulic pumps consist of several important components that contribute to their operation:
- Pump Housing: Contains the internal parts of the pump.
- Rotors or Pistons: The components that create fluid flow and pressure.
- Shaft: Connects the pump to the motor or engine, providing mechanical power.
- Seals and Bearings: Ensure smooth operation and prevent fluid leakage.
- Inlet and Outlet Ports: Allow fluid to enter and leave the pump.
5. Applications of Hydraulic Pumps
Hydraulic pumps are used in a wide range of industries and applications where high force and precision are required. Some of the most common applications include:
a) Construction and Heavy Machinery
Hydraulic pumps power excavators, bulldozers, cranes, and loaders, providing the necessary force for lifting and moving heavy loads.
b) Automotive Industry
In vehicles, hydraulic pumps are essential for power steering systems, hydraulic brakes, and suspension systems. They ensure smooth and efficient operation of these components.
c) Manufacturing and Industrial Equipment
Hydraulic pumps are widely used in industrial equipment such as presses, injection molding machines, and conveyor systems. They provide the precise control and power needed for manufacturing processes.
d) Agriculture
Hydraulic systems play a key role in agricultural machinery, such as tractors, harvesters, and irrigation systems. Hydraulic pumps are responsible for controlling attachments like plows, lifts, and loaders.
e) Marine and Aerospace
In marine and aerospace industries, hydraulic pumps are critical for controlling systems such as steering, landing gear, and propulsion systems.
6. Factors to Consider When Choosing a Hydraulic Pump
When selecting a hydraulic pump, several factors must be taken into account to ensure optimal performance and longevity:
- Pressure Requirements: Determine the maximum pressure your system requires and choose a pump that can handle those demands.
- Flow Rate: The pump should provide the appropriate flow rate to meet the needs of your hydraulic system.
- Fluid Viscosity: Ensure the pump can handle the viscosity of the hydraulic fluid you are using.
- Efficiency: Consider the efficiency of the pump to minimize energy consumption and maximize output.
- Maintenance and Durability: Choose a pump that is easy to maintain and built to last in your specific working environment.
7. Maintaining Hydraulic Pumps
Proper maintenance is crucial for the longevity and efficiency of hydraulic pumps. Here are some maintenance tips:
- Regular Fluid Checks: Monitor and maintain proper hydraulic fluid levels. Using clean and correct fluid ensures smooth operation and reduces wear.
- Inspect Seals and Bearings: Regularly check for wear or leaks in seals and bearings, as these are common points of failure in hydraulic pumps.
- Clean Filters: Hydraulic systems often include filters to remove contaminants from the fluid. Keeping these filters clean ensures that the pump runs efficiently and minimizes the risk of damage.
8. Conclusion
Hydraulic pumps are vital components in various industries, providing the necessary force to move fluids and power machines. Whether it’s a gear pump in an agricultural tractor or a piston pump in a heavy-duty construction crane, these devices are essential for countless applications. Understanding the different types of hydraulic pumps and their functions can help you make informed decisions when selecting the right pump for your specific needs. By choosing a high-quality, well-maintained hydraulic pump, you ensure optimal performance and efficiency in your operations.